Innoform veranstaltet am Donnerstag, 9. / Freitag, 10. Februar 2023 das 20. Inno-Meeting – das jährliche Branchentreffen für Folienverpackungshersteller, ihre Kunden und Lieferanten. Das Motto in diesem Jahr lautet Alles im Kreis und digital?!
Neben den Anstrengungen, die Kreislaufwirtschaft mit Folienverpackungen zu ermöglichen, drängt ein zweiter Mega-Trend ins Bewusstsein der Entscheider von Folienherstellern und Abpackern gleichermaßen – die Digitalisierung. Spannend wird es, wenn beides zusammen gedacht wird.
Da die Anzahl der Teilnehmer auf 160 vor Ort beschränkt ist, wird zusätzlich ein kostenpflichtiger Livestream angeboten. Neu ist auch die Möglichkeit der Table-Top Ausstellung – live und im Livestream. Netzwerkmöglichkeiten zwischen Vor-Ort-Teilnehmern, Ausstellern und Livestream-Teilnehmern werden durch die neue Event-Plattform ermöglicht.
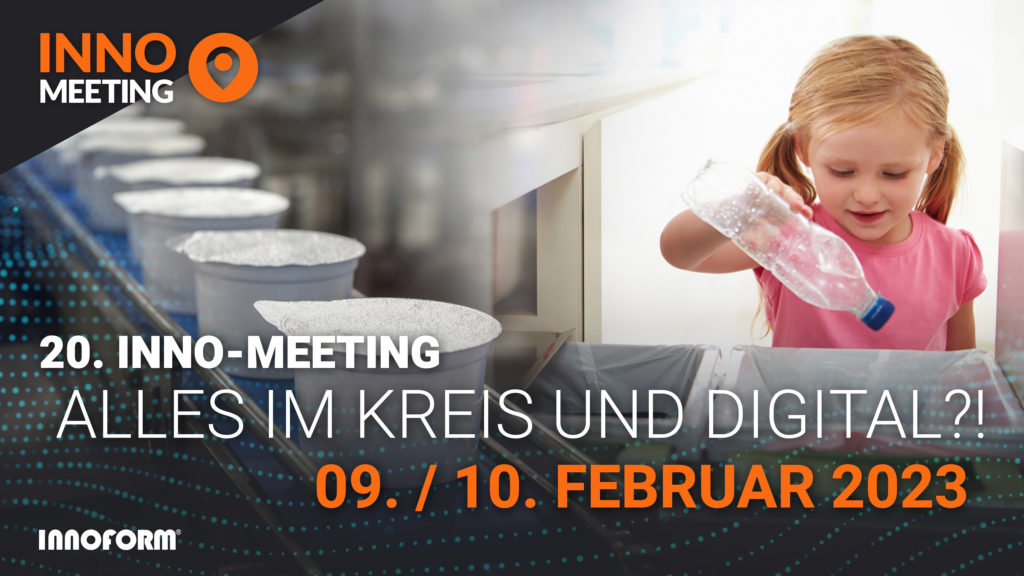
Inhalt der Veranstaltung
Flexible Verpackungen bieten viele Funktionen in dünnsten Schichten. Aber welche benötigt man wirklich im Detail, und wie erzeuge ich optimal welche Eigenschaften? Welche Trends drängen Flexpack-Entwickler und Markeninhaber? Wie entwickelt sich das Image der Folienverpackungen beim Verbraucher, und welche Rolle kann die Folien herstellende Industrie dabei spielen?
Seit Jahren dreht sich alles um Kreislaufwirtschaft – das ist gut. Doch alle anderen Features von Verpackungen entwickeln sich auch weiter. Neu ist dabei, vom Ende her zu denken und die Verwertung an den Anfang der Überlegungen zu bringen.
Ohne Glanz, Transparenz, Lichtschutz, Barriere, Bedruckbarkeit, Easy-Opening oder auch Robustheit aus dem Blickfeld zu verlieren, versuchen viele, Flexpack neu zu denken.
Wann sprechen unsere Verpackungen zu uns? Und welche weiteren digitalen Dienste übernehmen demnächst Codes auf Verpackungen? Welche Fortschritte und Verbreitung zeigt der Digitaldruck? Was macht Cradle2Cradle mit Druckfarben-Herstellern, und warum ist Nachhaltigkeit langfristig effizient? Wie digital sind eigentlich heute Veredelungsmaschinen?
Wie verändert virtuelle Realität (VR) die Flexible Verpackung der Zukunft? Kommt das Metaversum auch in die Verpackungsdruckereien und Extrusionsbetriebe? Wie wird die Digitalisierung und wie die Kreislaufwirtschaft Verpackungen verändern?
Und dann fragen wir uns noch, was eigentlich Bio-Ökonomie und neue Geschäftsmodelle an Impulsen für Folienveredler bringen können. Diskutieren Sie mit und profitieren Sie von den einzigartigen Teilnehmer*innen, Vorträgen und Referent*innen des 20. Inno-Meetings in Osnabrück.
Weitere Informationen, Anfragen zu Ausstell-Möglichkeiten und Teilnehmer-Registrierungen sind unter http://im.innoform.de möglich.