4. Teil: Häufig verwendete Folien zum Drucken und Kaschieren.
BARRIEREFOLIEN IM HINBLICK AUF VERARBEITUNG UND ANWENDUNG – EIN KOMPRIMIERTER ÜBERBLICK
von Karsten Schröder und Ansgar Wessendorf
Im vierten Teil dieser Artikelserie über die marktüblichen Arten und Typen synthetischer Folien (Kunststofffolien) zur Herstellung von Lebensmittelverpackungen stehen die Barrierefolien, die vor allem In Kaschieranwendung einen stetig wachsenden Anteil ausmachen.
Was verstehen wir heute unter Barriere in Bezug auf Folien, die für die Veredelung von Lebensmittelverpackungen gedacht sind? Versucht man in Lexika Definitionen hierfür zu finden, so sind diese sehr vielfältig. Begriffe wie:
– Hindernis
– Sperre
– Schranke
– Wellenbrecher
findet man z.B. in der online Enzyklopädie Wikipedia. Alles diese Begriffe beschreiben auch die Funktion, die eine Barriere für Folienverpackungen aufweisen soll.
Eine der wesentlichen Funktionen einer Folienverpackung ist naturgemäß der Produktschutz und die Abschirmung zur Umwelt. Aber auch das Fernhalten von Stoffen aus der Folie selbst wird immer häufiger – gerade bei Lebensmittelverpackungen – zur Nebenaufgabe. So können beispielsweise „Schadstoffe“ aus weiter außen liegenden Schichten der Verpackungsfolie durch eine innen liegende Barriereschicht dazu führen, dass diese Stoffe nicht mehr auf das verpackte Gut übergehen können. In Einzelfällen kann nur so die Gesetzgebung eingehalten werden. Hierzu werde ich im weiteren Verlauf näher eingehen.
Zunächst einige Bemerkungen zur Barriereberechnung. Grundsätzlich lassen sich heute Barriereeigenschaften von vielen Materialien rechnerisch gut abschätzen. In diesem Artikel werden wir aber mehr auf die praxisnahen Messungen und Füllgutschutz eingehen. Hier aber einige Grundlagen für den Praktiker, die jeder Barrierefolien-Hersteller kennt:
1. Barriere
Die Barriere setzt an drei Schritten zusammen (mache Literaturstellen nennen auch noch eine vierte – die Absorption, die wir hier auslassen möchte, da sie in der Praxis mehr verwirrt als nützt, bei akademischen Betrachtungen aber durchaus relevant sein kann).
a. Adsorption – das Anlösen des „Permeanden= Stoff der durchdringen kann/wird“
Damit ist also die Aufnahme des z.B. Gases Sauerstoff O2 gemeint, die direkt an der Oberfläche der Folie geschieht.
b. Diffusion – das Durchdringen des z.B. O2 durch die Folie, nachdem er in die Folie eingedrungen ist
Hier spielt primär die Diffusionskonstante eine Rolle, die Material abhängig ist
c. Desorption – Das Verlassen des Sauerstoffs der Folie – das „Ausdringen“ ist der dritte, der Adsorption umgekehrte Schritt, der die gesamte Permeation bedingt/beschreibt.
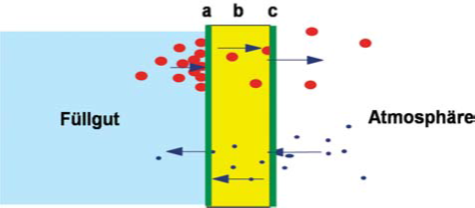
Abbildung 1 schematische Darstellung der Permeation von innen nach außen und von außen nach innen
2. Einflussfaktoren:
Die Verbesserung der Barriere ist möglich, indem man einen oder alle drei Schritte so verändert, dass der Permeand langsamer oder gar nicht mehr hindurch permeieren kann. Man kann also entweder die Adsorption reduzieren oder unterdrücken. Diese geschieht z.B. durch Metallisierungen, Lackierungen oder andere Oberflächenbehandlungen wie chemisch reaktive Prozesse. Alternativ dazu kann die Diffusion durch die Veränderung des Materials beeinflusst werden, um eine günstigere Diffusionskonstante zu erhalten muss in jedem Fall der Werkstoff gewechselt oder verändert werden. Auch das Verhältnis beispielsweise beim EVOH Copolymer zwischen Ethylen und Vinylalkohol verändert die Barriereeigenschaften aufgrund der veränderten Diffusion deutlich. Faustregel ist: Je mehr Vinylalkohol (VOH) desto besser die Barriere gegen Sauerstoff. Je mehr Ethylen €, desto besser ist die Feuchtigkeitsunempfindlichkeit der Folie hinsichtlich Sauerstoffpermeation. Dazu werden wir im abschnitt Barrierematerialien aber detaillierter zurück kommen.
3. Durchbruchzeit
Als Durchbruchzeit kann man die Zeit beschreiben, die es dauert, bis genauso viele Sauerstoffatome außen in die Folie eindringen, wie innen austreten. Man beschreibt hiermit also die Zeit, die es dauert, bis ein Gleichgewichtszustand erreicht ist, der primär vom Konzentrationsgefälle des Permeanden innen zu außen und dem Klima abhängt.
Die Steigung der Summenkurve gibt dabei die Permeationsrate an. Legt man an den linearen Verlauf eine Tangente an, so gibt der Schnittpunkt mit der X-Achse die Durchbruchzeit an, die zwischen Sekunden und einigen Tagen liegen kann und somit nur für kurz haltbare Lebensmittel bei der Barriereauslegung bedeutsam ist.

Abbildung 2 Durchbruchzeit und Permeationsrate schematisch dargestellt
2 Definition Dichtigkeit
Als Überbegriff der Permeation fungiert die Dichtigkeit. Dichtigkeit oder Dichtheit beschreiben bei Verpackungen das gesamte System – also die Permeation durch das Material aber auch Einflüsse durch Siegelnahtfehler oder Löcher in der Verpackung. Nun beschreiben Dichtheitsprüfungen einige Zehnerpotenzen geringere Genauigkeiten des Stoffdurchtritts in eine Verpackung als die Permeation, weshalb der Schluss nahe liegt, dass zuerst einmal eine Verpackung dicht (verschlossen) und unbeschädigt sein muss, bis man über Permeation nachdenken sollte.
3 Barriereeigenschaften einiger bedeutender Folien
3.1 Das EVOH (Ethylen Vonyl Alkohol)
Eine der bedeutendsten Barrierematerialien aus Kunststoff ist nach wie vor das EVOH, das sich durch gute Transparenz, gute Verarbeitbarkeit, hervorragende Sperrwirkung gegen Sauerstoff und Aromen sowie Thermo-Verformbarkeit auszeichnet.
Wo Licht ist, ist leider auch Schatten. So hat das EVOH ein bisher ungelöstes Problem mit Feuchtigkeit. Natürlich gibt es Konstruktionen und Lebensmittel, die hier unproblematisch sind, dennoch ist stets drauf zu achten, dass EVOH in möglichst trockenem Zustand seine volle Barrierewirkung entwickelt. Welchen Einfluss Feuchtigkeit und Temperatur auf die Barriere von EVOH Verbundfolien haben kann, zeigt das folgende Diagramm.
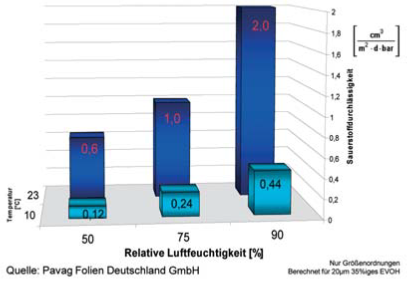
Abbildung 3 Folie aus dem Seminar Grundkurs Kaschiertechnologie: Einfluss von Temperatur und Feuchtigkeit auf Sauerstoffbarriere vom EVOH
An dieser stelle werden wir nicht näher auf die enormen Einflussfaktoren auf die Barrierewirkung eingehen. Weitere Informationen finden Sie u.a. unter http://www.eval.be/web/index.asp?lang=de&ut=L .
Für den Weiterverarbeiter, wie Drucker und Kaschierer, ist auf jeden Fall darauf zu achten, das wenig Feuchtigkeit in der Anwendung an die EVOH Schicht gelangt. Das ist auch ein Grund, warum EVOH immer im Verbund (z.B. mit PE, PP oder PA) verarbeitet wird.
3.2 Typische Anwendungen und Eigenschaften von EVOH-Verbundfolien
Eine typische Anwendung von EVOH Folien sind die vielfältigen MAP-Verpackungen (modified atmosphere packaging). Hier spielt das thermoverformbare EVOH seine ganze Stärke aus. Zum einen kann durch Wechsel der EVOH Copolymer-Type die Sauerstoffdurchlässigkeit (OTR=Oxygene transmission rate) eingestellt werden oder einfach über die Schichtdicke. Aufgrund seiner Verformbarkeit wird es gerne in Unterfolien eingesetzt, wenn ein besonders O2 empfindliches Produkt verpackt werden soll. Aber auch in den Deckelfolien wir traditionell EVOH eingesetzt, obwohl heute auch weniger feuchtigkeitsempfindliche Materialien wie SiOx bedampfte Folien oder Metallisierungen verwendet werden. Insbesondere für feuchte Füllgüter sind diese nicht organischen Bedampfungen (nicht aus Kunststoff bestehenden) Folien wirksamer.
So finden sich heute u.a. in vielen Wurst-/Fleisch- oder auch Tubenlaminaten EVOH Barrieren.
3.3 EVOH als funktionelle Barriere
Das Lebensmittelbedarfsgegenständerecht sieht europaweit vor, dass „Schadstoffe“, die in Folien technisch unvermeidbar sind, durch s.g. funktionelle Barriereschichten gesperrt werden können, so dass dann in der Lebensmittel abgewandten Seite höhere Konzentrationen von „Schadstoffen“ toleriert werden können, wenn nachgewiesen wird, dass die funktionelle Barriere diese Stoffe vom Lebensmittel fern hält/sperrt.
Auch in solchen Anwendungen findet EVOH Einsatz. Zum Beispiel die immer häufiger eingesetzten Wiederverschluss-Systeme, die in der Regel aus leicht migrierenden Komponenten formuliert werden, müssen in ihrer Migrationsneigung ins Füllgut gebremst werden. Diese Aufgabe übernimmt in einigen Fällen eine sehr dünne (1 – 3 µm) EVOH Sperrschicht, die quasi nebenbei natürlich auch die Sauerstoffbarriere erhöht und somit zu einer längeren Haltbarkeit des verpackten Lebensmittels führt.
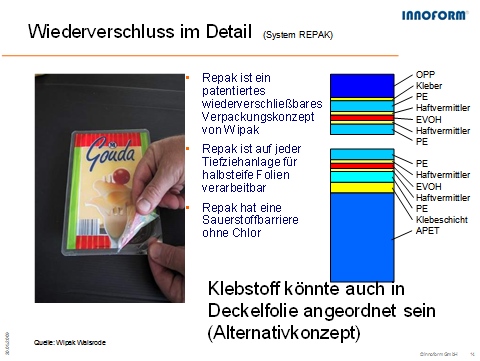
3.4 Bedampfungen
Eine weitere Möglichkeit Folien hinsichtlich Ihrer Barriereeigenschaften erheblich zu verbessern ist die Bedampfung. Eine Untergruppe stellt hier die Aluminium-Metallisierung dar, die im großtechnischen Maßstab eingesetzt wird. Diese silbrige Folienbeschichtung führt zudem zu einem oft ausreichendem Lichtschutz.
Zudem finden transparente, anorgansische Bedampfungsschichten immer mehr Einsatz. Hier erwähnen wir nur kurz SiOx und AlOx als die häufigsten. Aufgrund der Oxodation behalten die Stoffe ihre Sperrwirkung, werden aber hoch transparent. Sie lassen sich problemlos mit geeigneten Druckfarben bedrucken.
Nähere Details können jederzeit von den einschlägigen herstellern oder bei Innoform erfragt werden.
4 Barriereeigenschaften einiger handelsüblicher Folien
Vergleicht man nun einmal typische Druckträgerfolien hinsichtlich ihrer Barriereeigenschaften, so lässt sich daran einiges an physikalischen Grundlagen erklären. Betrachten wir im Folgenden einmal diese typischen Folien in ihren handelsüblichen Dicken:
PP-BO 20 µm
PET-BO 12 µm
PA-BO 15 µm= Polyamid biaxial orientiert
PA-C 20 µm = Polyamid cast (Gießfolie nicht orientiert)
PET-BO 12 µm mit SiOx Beschichtung
Hier einige Daten, wie einige handelsüblichen kaschierfplien im Vergleich bei OTR- Betrachtungen abschneiden. Dieses sind nur Richtwerte und Spezialtypen weichen natürlich im Detail ab. Die Tendenz bleibt aber.
Abbildung 4 Sauerstoffdurchlässigkeit handelsüblicher kaschier-/Druckfolien
Betrachtet man hier die Sauerstoffdurchlässigkeit im Vergleich, so wird deutlich, dass mit zunehmender Polarität des Werkstoffes die Permeation abnimmt. Am schlechtesten schneidet das PP-BO ab, das kaum eine Sperrwirkung gegen O2 zeigt. Das PET und das PA hingegen schon als zumindest O2 Bremsen bezeichnet werden können. In den Bereich echter Barriere dringt aber nur das PET-BO mit SiOx Beschichtung vor.
Betrachtet man nun die Wasserdampfdurchlässigkeit in der folgenden grafik, wird schnell klar, dass bei den organischen, Kunststoffschichten sich das Bild umkehrt. Bei der anorganischen SiOx Schicht hingegen, bleibt das Niveau niedrig.
Abbildung 5 Wasserdampfdurchlässigkeit handelsüblicher kaschier-/Druckfolien
Die genannte SiOx und AlOx Schichten sind genau wie Aluminium-Metallisierungen deshalb in ihrer dünnen Ausprägung spröder als organische/Kunststoffschichten. Das bedeutet für den Drucker und Kaschierer, aber auch für das Logistikteam besondere Sorgfalt.
So sind beispielsweise die transparenten Barrieren nach der Herstellung „vorgespannt“ auf der Folienoberfläche. Dehnt man nun die Folie extrem, so können die dünnen Schichten brechen und teilweise Ihre Barrierewirkung verlieren.
Abbildung 6 Schematische Darstellung der Eigenspannung von anorganischen Beschichtungen
Natürlich kann auch eine schwer drehende Welle oder ein kratzendes Entionisierungs-Selbstkonstruktion zu kleinsten Kratzern und somit Fehlstellen führen. Diese fehlstelölen sieht man erstens nicht und zweitens sind sie nur durch aufwendige Permeationsmessungen statistisch zu erfassen.
Die Lösung ist wie so oft Wissen und Sorgfalt beim Umgang.
4.1 Auf welcher Seite drucke ich gerade?
Diese Frage hat sich vielleicht schon mancher Drucker, Kaschierer und Betriebsleiter gestellt, wenn er bedampfte, transparente Folien verarbeitet hat. Hierzu zum Schluss noch ein kurzer Tipp:
Um die zu bedruckende Seite schnell und sicher zu bestimmen benötigen Sie nicht merh als das Wissen, einen Eimer mit Wasser und einen Schwamm. Hängt die SiOx oder AlOx Rolle erst einmal in der Maschine, schlagen Sie ca. 30 cm des Rollenendes um und benetzen mit dem angefeuchteten Schwamm die Folienbahn auf der Vorder und Rückseite.
Auf der Seite, auf der das Wasser besser benetzt, sollten Sie stets drucken, denn das ist die bedampfte Schicht, die im Zwischenlagendruck geschützt werden muss.
Aber Achtung. Die Oberflächenspannung ist oft so hoch, dass nicht alle farben gut ausdrucken und haften. Fragen Sie hierzu Ihren Farb-/Folienlieferanten, der Ihnen geren Auskunft über getestete Systeme geben wird.
4.2 Vorbehandlungsintensitäten
Hier noch eine Tabelle, welche Vorbehandlungsintensitäten die besprochenen Folien haben. Als Drucker und Kaschierer wissen Sie natürlich, dass wir mindestens 38 mN/m benötigen, um gut zu Benetzen und Haftung zu erzielen. Wie wir das schaffen berichten wir in einem der nächsten Artikel.
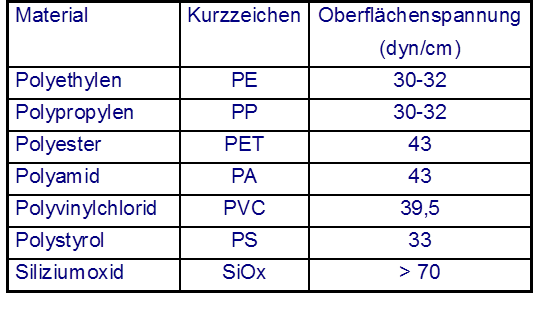
[Artikel Serie 1-8 “Drucken und Kaschieren” wird fortgesetzt]
Innoform auf 
Kontakt:
Innoform GmbH Testservice
Industriehof 3,
26133 Oldenburg
TS@innoform.de
www.innoform.de