Eine Möglichkeit, Lebensmittel haltbarer zu machen, ist das Entkeimen unter bestimmten Temperatur-/Zeit-Kombinationen
(siehe auch https://de.wikipedia.org/wiki/Sterilisation). Dazu gehören Pasteurisations- und Sterilisationsprozesse, die zwar eine Verlängerung des Mindesthaltbarkeitsdatums bewirken, jedoch auch gleichzeitig eine enorme Belastung für das Verpackungsmaterial durch die Temperatur- und Feuchtebehandlung bedeuten. Die Hauptfunktion der Verpackung besteht darin, das Produkt zu schützen. Daher muss sichergestellt sein, dass das Material für diese Prozesse auch geeignet ist.
In der industriellen Fertigung werden Autoklaven eingesetzt, um die Lebensmittel zu sterilisieren. Es handelt sich dabei um einen Behälter, der gasdicht verschlossen werden kann, um Stoffe, z. B. Lebensmittel, im Überdruckbereich thermisch zu behandeln (siehe auch Wikipedia: https://de.wikipedia.org/wiki/Autoklav).
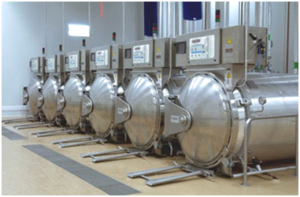
Da Erprobungstests in den groß-industriellen Anlagen aufwendig und somit kostenintensiv sind, können grundsätzlich die Materialeigenschaften zunächst auch im Labormaßstab untersucht werden. Der Innoform Testservice nutzt dafür einen Autoklaven, der analog zu den groß-industriellen Anlagen mit Heißwasser- bzw. Kühlwasserberieselung arbeitet, und bei dem der Gegendruck gesteuert werden kann, damit eventuelle Gaspolster in der zu sterilisierenden Packung nicht zum Platzen führen.
Die Temperaturprogramme können frei definiert werden, so dass alle in der Praxis gängigen Programme der Pasteurisation und Sterilisation auch im Labor durchgeführt werden können.
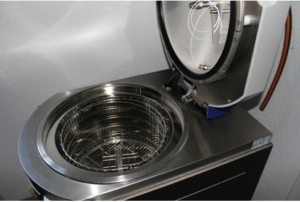
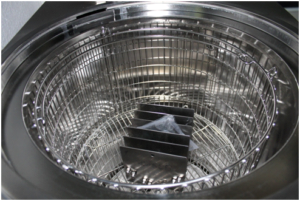
Folgende Materialeigenschaften werden häufig im Vergleich zu den Ausgangseigenschaften vor Sterilisation untersucht, da sie als kritisch für die Praxis zu bewerten sind:
- Dimensionsstabilität/Optik
- Verbundhaftung zwischen den einzelnen Materialschichten
- Siegelnahtfestigkeit
- Sauerstoffbarriere: Beim Einsatz von feuchtigkeitsabhängigen Werkstoffen,
wie z. B. EVOH und PA, sinkt die Gas-Barrierewirkung des Materials durch den Sterilisationsprozess häufig. Wie stark der Einfluss ist bzw. wie lange es dauert, bis das Material sich davon „erholt“, kann durch eine Abklingkurve gemessen werden, indem die Permeationsmessung unmittelbar nach der Sterilisation gestartet wird.
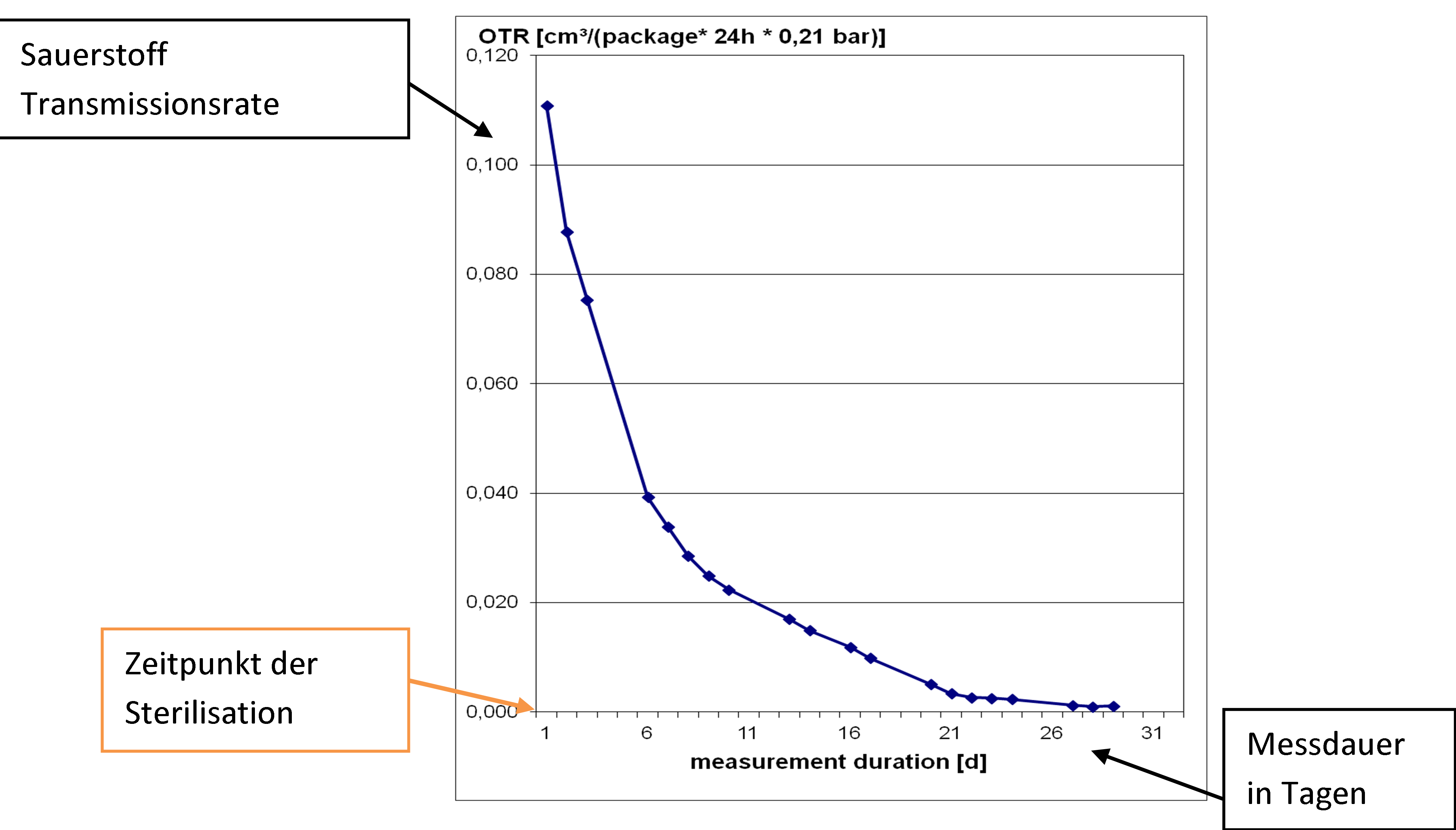
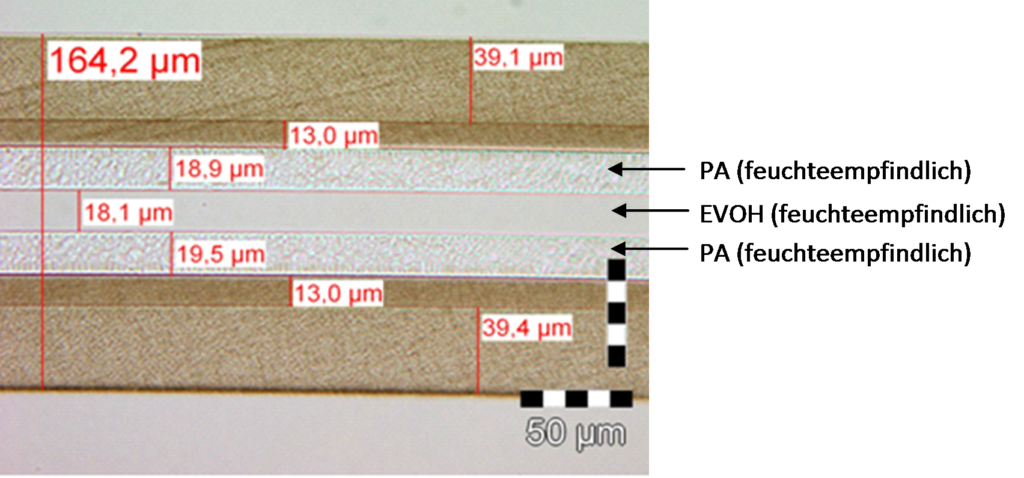
Untersuchung des Einflusses auf die lebensmittelrechtliche Eignung durch Autoklavierung
Der Übergang von Substanzen aus Verpackungsmaterialien auf ein Lebensmittel ist von vielen Parametern abhängig. Neben z. B. der Löslichkeit der Substanzen, dem pH-Wert und den Diffusionseigenschaften der verwendeten Materialien spielt die Temperatur eine entscheidende Rolle. Eine Temperaturerhöhung führt zur Zunahme der Reaktionsgeschwindigkeit. Als Faustregel geht man bei einer Temperaturerhöhung um 10° C (exakter10 K) von 10 K einer Verdopplung der Reaktionsgeschwindigkeit aus (Arrhenius-Regel). Daher kann es für Sterilisationsanwendungen sehr wichtig sein, die Migration bei erhöhten Temperaturen zu messen.
Für die Herstellung von Kaschierklebern auf Polyurethan-Basis werden Isocyanate als Ausgangssubstanzen verwendet. Beim Erwärmen der daraus hergestellten Verbundfolien kann der Kleber durch Hydrolyse zurückspalten, und es können sich primäre aromatische Amine bilden, obwohl der Kleber zuvor ausgehärtet war und mit Standardtests (z. B. 2 h/70° C) Aminfreiheit bestätigt werden konnte. Einige Vertreter der Substanzgruppe der primären aromatischen Amine (paA) sind bekanntlich krebserzeugend; daher ist die Auswahl der richtigen Klebstoffe für Sterilisationsanwendungen essentiell, wie auch die Überprüfung der Klebstoffe unter realistischen Temperaturbedingungen.
Für Sterilisationsverfahren wurde beobachtet, dass die Ersatzbedingungen von 4 h bei Rückflusstemperatur geringere Amin-Migrationswerte als eine Sterilisation von 30 min bei 121° C ergeben können. Die Eignung eines Kaschierklebers kann nur durch eine Prüfung auf paA-Migration nach Sterilisation im Autoklaven und Einhaltung der Grenzwerte unter diesen Praxisbedingungen sichergestellt werden.
Damit Sie Ihre Produkte nicht in großen Industrieanlagen prüfen müssen, betreiben wir seit einiger Zeit einen modernen Laborautoklaven mit aktueller Steuerungs- und Kühltechnik, so dass wir industrielle Sterilisationsprozesse schnell und kostengünstig simulieren können.
Bei Interesse sprechen Sie uns gern an:
Innoform Testservice GmbH
Matthias Bösel
Industriehof 3
26133 Oldenburg
Tel.: +49 441 94986-0
Fax: +49 441 94986-29
www.innoform-testservice.de
E-Mail: matthias.boesel@innoform.de